Eurotec's long term test for corrosion resistant screws
Eurotec's long term test for corrosion resistant screws
Corrosion protection is a key issue in timber construction. Eurotec relies on high quality materials and a high-quality surface coating to ensure long term durability and corrosion resistance of the fasteners for our customers. When the screw meets these critical properties, the life of the fastener is extended and its performance in the various applications is improved. As a result, the screw can be used to make long-lasting connections in construction projects ranging from timber construction to industrial applications.
An overview of the different corrosion categories
The question arises as to which screw is the right one for the planned construction project. In order to determine the correct material and coating, there are clearly defined parameters. First, there are the service classes 1 to 3 according to Eurocode 5 EN 1995-1-1:2010-12, which determine where the screw can be used: internally, externally, structurally protected or externally unprotected.
Second, there is Corrosion Category C, which is governed by DIN EN 14592:2022. This corrosion category specifies what the climate may be like, as well as the salt and pollutant content of the air. Accordingly, this category regulates the atmospheres in which the screw is installed. There is also an alternative to the C category for stainless steel screws — the CRC category, which is governed by DIN EN 1993-1-4:2015-10. This category also addresses the risk of exposure.
In addition to the corrosion of the screw, there is also corrosion in the wood of a timber structure. This is determined by the T-category according to DIN EN 14592:2022. The T-category indicates which types of wood can be used depending on the pH and moisture content of the environment.
For more information on this subject, please refer to pages 16 to 19 of our Timber Fasteners Catalogue:
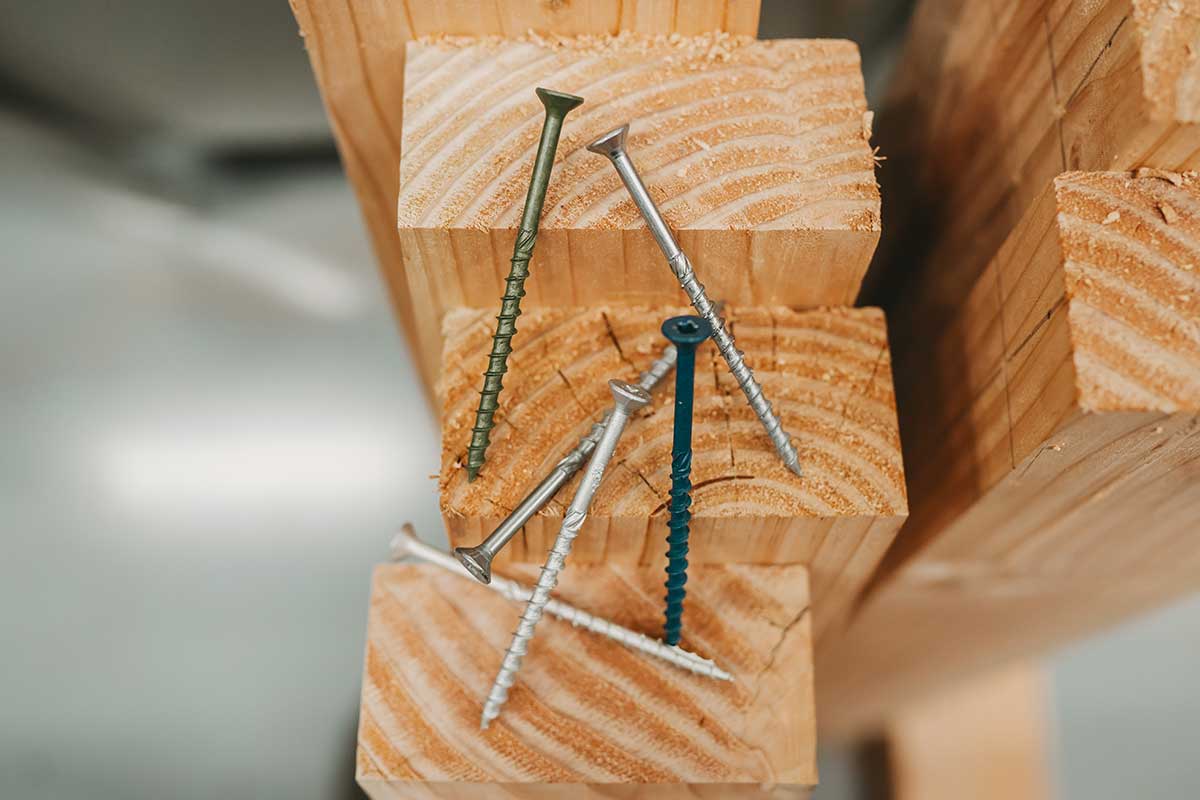
Why does Eurotec test?
In a location with a high salt content in the air, such as by the sea or in a heavily polluted industrial area, C4 corrosion resistance is required and T4 if wood with a high acid content is used. These high values are normally only achieved with A2 or A4 stainless steel screws and not with carbon steel screws. However, stainless steel screws are in the higher price range and cannot be hardened.
Eurotec has therefore set itself the task of finding a screw coating that achieves the required values without having to resort to stainless steel.
What coatings do we test?
For the test, we screwed in Paneltwistec with a diameter of 5 and 6 mm and a length of 100 mm. The screws have six different coatings.
There are several test methods for this, which are defined in DIN EN 14592. As we only test inorganic coatings, the test methods for organic coatings are not covered.
Eurotec's four-year test
In a long-term test, the screws must be screwed into softwood beams. The wood must also meet at least T4 requirements. We have chosen Douglas fir for the test procedure. The wooden beams must be assembled using the EN ISO 8565:2011 test method and stored in an appropriate category C4 atmosphere. In addition, at least 10 test specimens must be weathered and 10 stored unweathered in order to obtain a comparative value.
The structure roughly explained:
The samples must be oriented at an angle of 45°, pointing horizontally upwards. To prevent splashing, the distance between the ground and the samples must be at least 0.5 metres. The distance between the samples should be such that there is no direct contact between them and no run-off water can pass from one sample to the other. The frame may be made of wood or metal, provided that it is sufficiently strong, weatherproof, and protected against corrosion. There must be no direct (electrical) contact between the samples and the frame. The individual screws must be screwed in at the end and edge spacings specified in EN 1995-1-1:2004.
The following first draft has been created with the above criteria in mind:
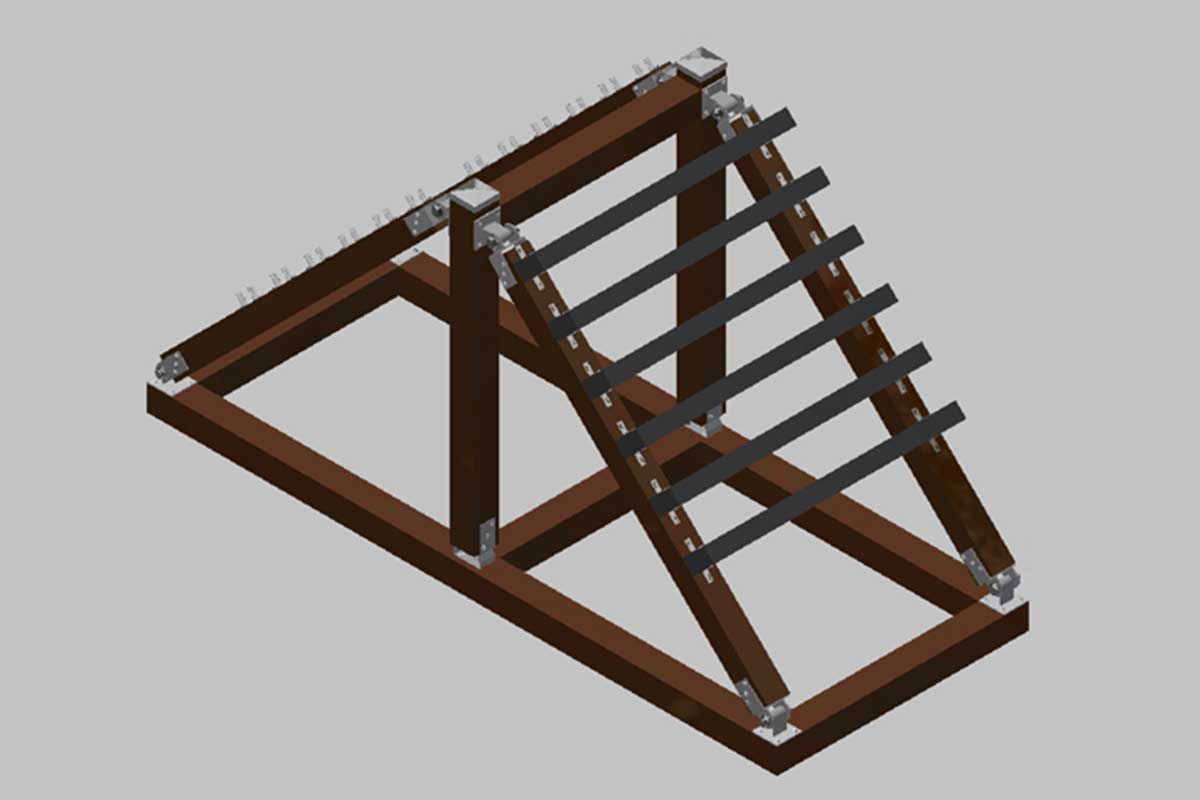
The design was then implemented, and the screws needed for the test were organized.
Location 1: Denmark near the coast
The scaffolding is close to the coast and therefore suitable for category C4, measured by the salt content of the air.
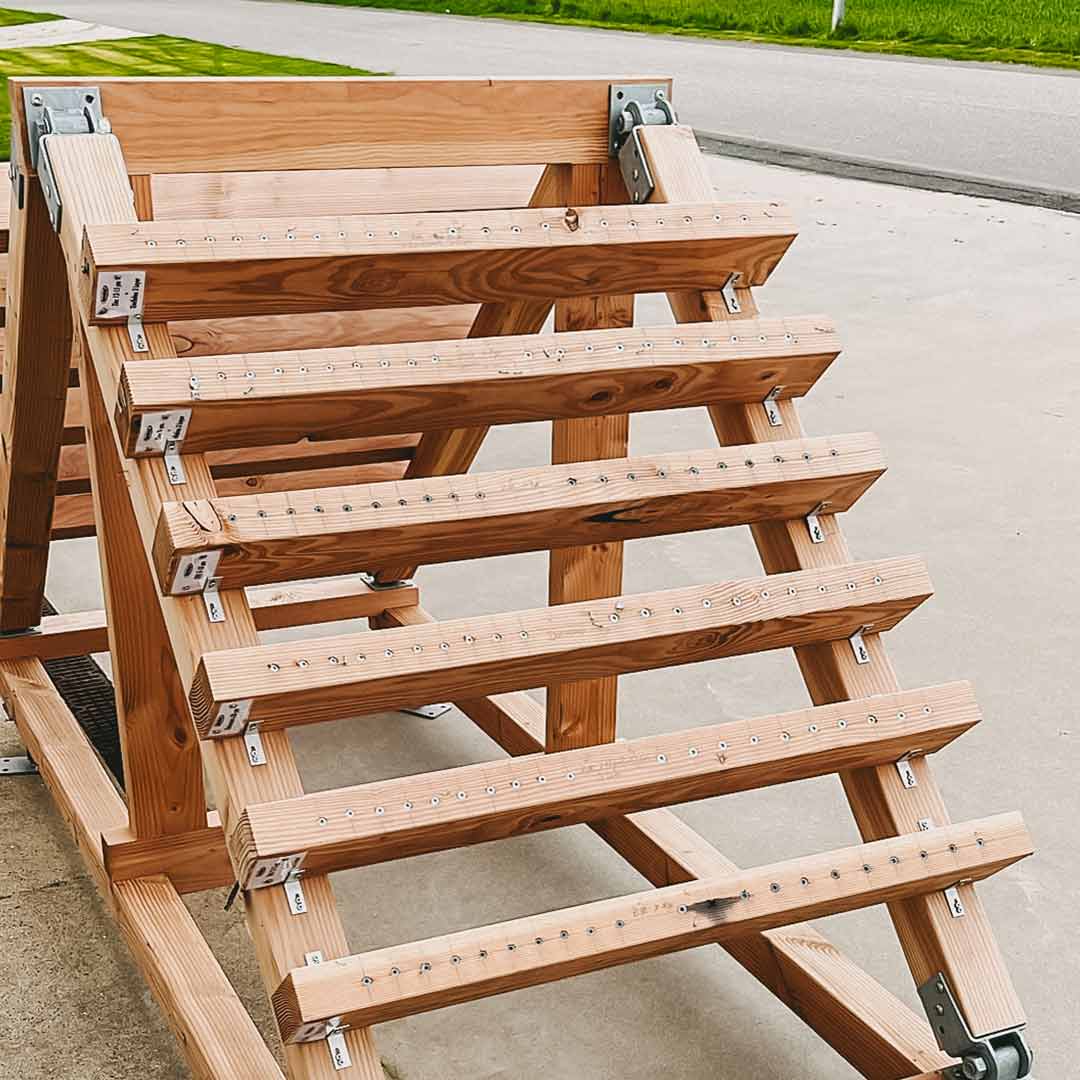
Location 2: The Eurotec company in Hagen
Eurotec is located in an industrial area and is therefore suitable for category C4 air pollution.
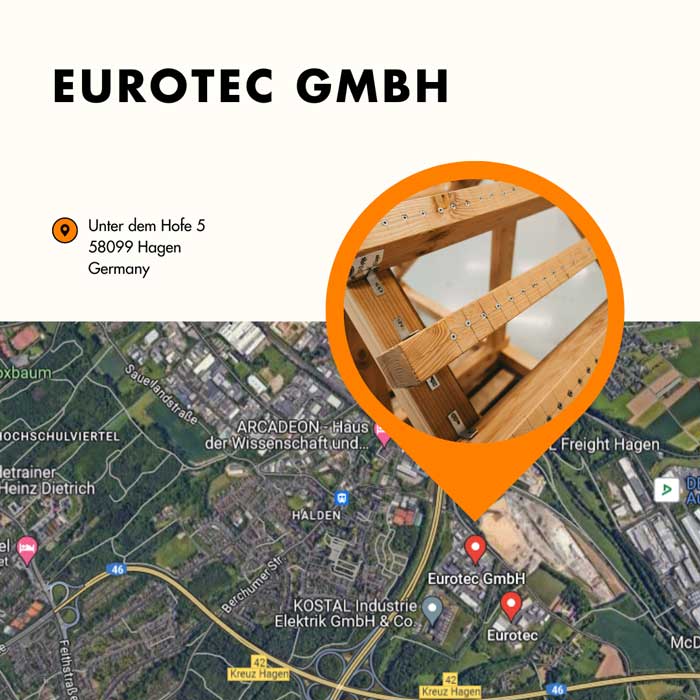
How is the evaluation done?
After four years, the coniferous Douglas fir is opened with a chisel to inspect the specimens inside. The specifications are deemed to have been met if no rust is visible around the entire circumference. It is also possible to check that the quality of the protective coating meets the specifications by carrying out a metallurgical test. This test can be used to demonstrate that the use of the bolt does not affect the quality of the protective coating.
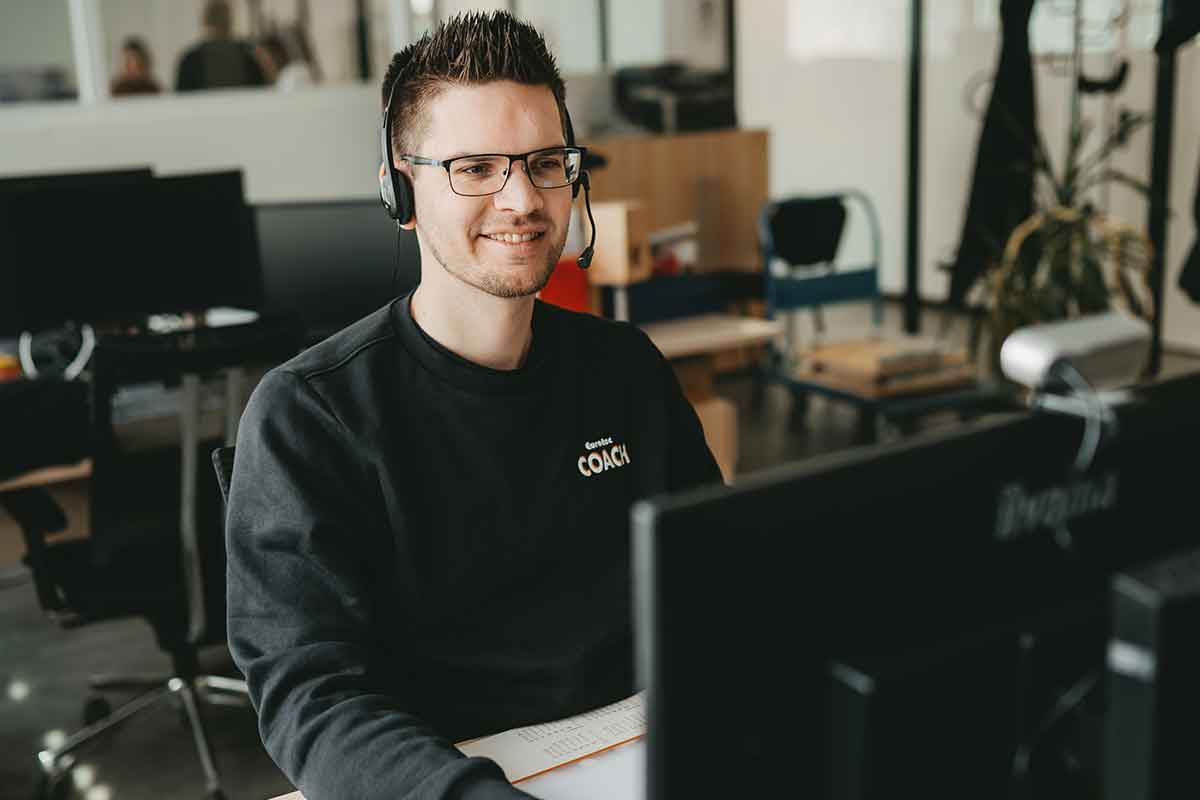
Do you have any technical questions?
We are happy to assist you with your construction project! Contact our technical department via email at technik@eurotec.team, call us at +49 2331 62 45-444, or use the free calculation software for planning.
Other technical articles
Here you will find further specialist articles with comprehensive content that you need to know on the construction site or for individual projects - regardless of whether you are just starting out or already have many years of experience.